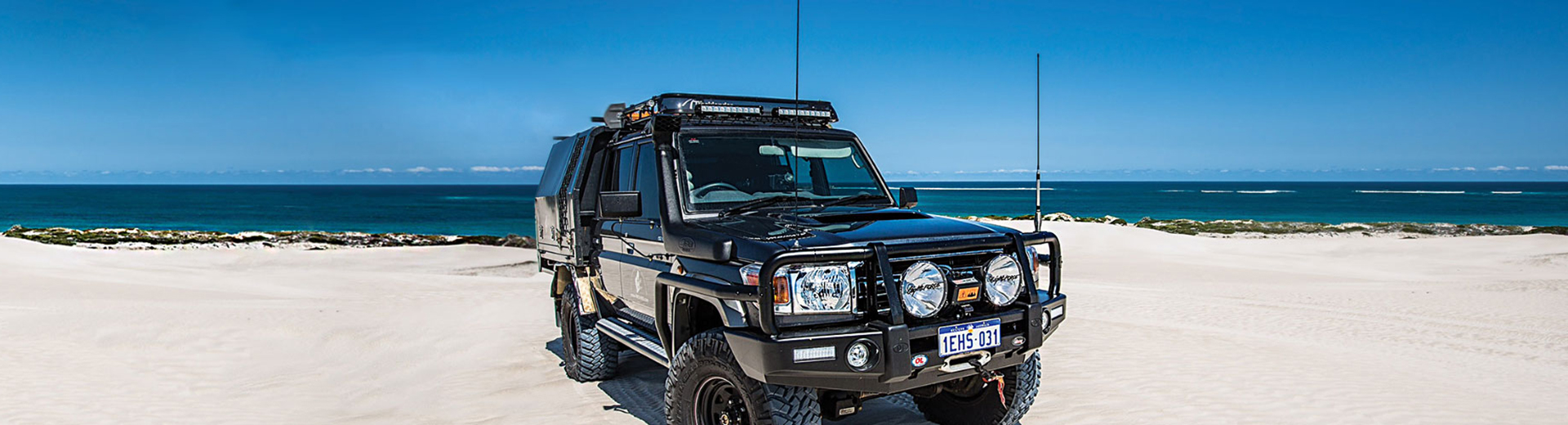
PROTECTION GEAR
Opposite Lock Protection Gear
Opposite Lock has a range of bullbars to suit your vehicle, including Steel, Alloy and Polyethylene. Each bar has their own benefits and Opposite Lock will help you make the right decision.
Bullbars are the staple of the 4x4 world, not only do they help protect your vehicle and its vital mechanics, they provide mounting options for other vehicle accessories including winches, lights, antannaes, they define the look of your vehicle and make it stand out from the rest.
Steel, Alloy or Poly, each bar has its benefits and Opposite Lock staff will be happy to explain them in detail. Come in store and get up close to see for yourself and get the right advice, every time.
The Opposite Lock Production Process
Designed in Australia using the latest vehicle scanning technology, for the most accurate and best fitting bullbars on the market.
Before a bullbar can be released to the public, it must first pass through a series of complex design, build, test, safety and production phases.
Opposite Lock bullbars only make it to market when they pass all of these strict internal policies and guidelines, so you know when you choose to have an Opposite Lock bullbar fitted to your vehicle, you’re getting the best.
3D VEHICLE SCANNING
The first step in the development of any OL bullbar is to digitally scan the physical front end of the project vehicle, this gives our engineers a perfect three dimensional representation of the vehicles front end.
AUTOCAD DESIGN
Engineers then use the 3D scan to design a bar that follows the natural contours of the vehicle, this process also eliminates potential fitment issues and unappealing joining gaps between the bar and chassis.
FITTING & TESTING
A test bar is manufactured to the engineers specifications and is both test fitted in our plant in Thailand and testing facilities in Australia. Engineers and fitment officers then compare notes and make refinements as needed.
PROTOTYPE
After the initial design is complete, a prototype is developed for ADR certification and testing. We also run the bar through our own real world field tests to measure vehicle response and make any alterations to the aesthetic should it be required.
SAFETY AND COMPLIANCE
The prototype is then independently tested to ensure it adheres to ADR69/00 (Full Frontal Impact Occupant Protection). Once the bar has passed
its ADR (Australian Design Rule) tests, it then goes back to our engineers for their final sign off.
FULL SCALE MANUFACTURE
After all previous steps are completed our bars are then ready to go to full scale production in our plant in Thailand.
Following a strict quality control procedure, they’re then shipped directly to our holding facilities in Australia.